Sprzęt schodzi z taśmy
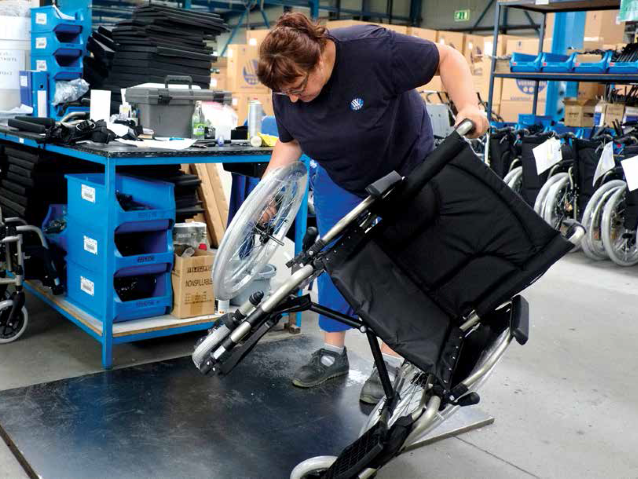
Rzadko kiedy trafia się okazja, by zobaczyć, jak wygląda produkcja wózków inwalidzkich. Integracja gościła w jednej z fabryk – z nowoczesnym parkiem maszynowym i w pełni zautomatyzowaną linią produkcyjną.
W Trzebnicy, zaledwie 13-tysięcznym miasteczku w wojewodztwie dolnośląskim, które prawa miejskie uzyskało w 1250 roku, znajduje się największy zakład sprzętu medycznego w Europie – z nowoczesnym parkiem maszynowym, specjalizujący się w produkcji wózków inwalidzkich i łóżek rehabilitacyjnych: firma Vermeiren.
Trzebnicka fabryka...
... (jeszcze pod nazwą Reha-Pol) powstała 21 lat temu, kiedy właściciel Vermeirena postanowił przenieść produkcję z drogiej Belgii do Polski. Korzyścią tej decyzji była nie tylko praca dla ok. 400 mieszkańców Trzebnicy i okolic, lecz przede wszystkim to, że polscy pacjenci i osoby z niepełnosprawnością uzyskali dostęp do kompleksowego zaopatrzenia w sprzęt rehabilitacyjny. Zapewnia to jednocześnie wysokiej jakości usługę serwisową z szybkim dostępem do części zamiennych. Stanowi atut i mocną stronę oferty firmy Vermeiren.
Integracja otrzymała pozwolenie na wejście na teren fabryki, do czterech dużych hal o łącznej powierzchni 20 tys. mkw. – ślusarni, lakierni, tapicerni i montowni. Z linii produkcyjnych schodzi tu rocznie – bagatela – ok. 60 tys. wózków i 15 tys. łóżek rehabilitacyjnych, z czego prawie jedna czwarta trafia na polski rynek. Tak wysoka sprzedaż świadczy o popularności produktów Vermeiren na świecie i w Polsce.
Ślusarnia to ogromna hala...
... o powierzchni 10 tys. mkw., w której obrabiane są wszystkie metalowe części i podzespoły do produktów producenta. Główne materiały, z których się tu korzysta, to stalowe rury i aluminiowe płyty. Cięcie, wycinanie otworów, wzorów i napisów, gięcie oraz spawanie, są całkowicie zautomatyzowane, wykonują je nowoczesne lasery i roboty. Kiedyś rurę cięto mechanicznymi piłami, a pocięte fragmenty trafiały na prasę – każdy otwór o innym rozmiarze wycinano na innej prasie, a każde działanie wiązało się z nowym jego ustawieniem na matrycy. Obecnie trzy duże laserowe maszyny (w październiku przybędzie czwarta) automatycznie tną i wycinają niezbędne otwory i wzory w rurze i profilach, oraz w blasze.
Ta technologia otworzyła w fabryce całkowicie nowe możliwości w projektowaniu i produkcji podzespołów i wyrobów, a także pozwoliła zaoferować klientom 5-letnią gwarancję na ramę każdego wózka inwalidzkiego. Wiele produktów zawdzięcza swój wygląd (design) właśnie tym laserowym maszynom. Część tak przygotowanych elementów trafia stąd na giętarki, które także automatycznie wyginają je do zaprogramowanego wcześniej wzoru. Tutaj kilku pracowników zakłada je na automaty i wciska przycisk, a po ich wygięciu przez maszynę, sprawdzają na specjalnym wzorniku, czy kształt elementu zgadza się ze wzorem.
Kolejnym etapem w procesie przygotowywania w ślusarni danej części pod końcowe urządzenie jest łączenie różnych detali za pomocą spawania. I ten proces odbywa się automatycznie – pracownik montuje na specjalnej matrycy odpowiednie detale, następnie umieszcza ją na stole spawalniczym, a spawalnicze roboty (inne do stali, inne do aluminium) łączą je ze sobą. Przygotowane w ten sposób podzespoły i ramy są gotowe do polakierowania i ze ślusarni trafiają do lakierni.
Lakiernia...
...a dokładnie linia lakiernicza jest oczywiście automatyczna i skomputeryzowana – centralny komputer definiuje i nadzoruje wszystkie procesy. Kilku pracowników wiesza na linkach elementy, które transportowane są na wyciągu przez kolejne pomieszczenia: myjnię, odtłuszczalnię, lakiernię proszkową oraz piec wygrzewający, a następnie je ściągają i wkładają do kontenera, który trafia do dużej hali montażowej.
Na kilku liniach montażowych grupy pracowników składają wózki, łóżka i sprzęt pomocniczy. Każda linia składa inny model wózka, łóżka, czy rowerka trójkołowego i podzielona jest na kilka części, w których pracownicy tam przydzieleni montują konkretne elementy urządzenia. Tutaj trafiają także z tapicerni (hala o powierzchni 2 tys. mkw.) wszystkie wyroby przygotowane przez pracowników: zszywaczy, zgrzewaczy i tapicerów.
Każda linia montażowa kończy się specjalną płytą do kontroli jakości każdego w pełni złożonego urządzenia, pracownik sprawdza, czy urządzenie trzyma wszystkie parametry i zawiera części zgodne z kartą kontrolną, a na końcu składa swój podpis. Z tego miejsca urządzenia trafiają do części hali, gdzie grupa pracowników zakłada na nie folię ochronną, a następnie pakuje w kartony i zawozi do magazynu. Magazyn jest niewielki jak na tak duży zakład. Okazuje się jednak, że większy nie musi być, ponieważ produkty są na bieżąco rozwożone – nie ma potrzeby ich długiego przechowywania.
– Cały proces produkcji w zakładzie na wszystkich etapach działa na zasadzie „Just-in-time”, czyli wszystko wykonywane jest na wyznaczony czas – mówi Robert Korzeniowski, dyrektor handlowy firmy Vermeiren. – Mniej więcej raz w miesiącu przywożona jest do nas pewna partia stali z Belgii, większość jednak jest od dostawców krajowych, którzy dzięki inwestycjom w nowoczesne technologie poprawili jakość i dostępność swoich produktów. Nie mamy też wielkich magazynów ani własnej floty transportowej, gdyż wyprodukowany sprzęt szybko jest rozwożony przez wynajętych dostawców transportowych do dystrybutorów w Polsce i do naszej centrali w Belgii. „Just-in-time” w naszej produkcji musi obowiązywać, ponieważ tworzymy bardzo wiele produktów. Wystarczy wspomnieć, że jeden model wózka wykonywany jest wielu wersjach – innych rozmiarach, kolorach, z różną tapicerką i opcjami.
W dziale projektowym...
... pięciu młodych inżynierów po studiach wzornictwa przemysłowego i budowy technologicznej maszyn, projektuje wyroby Vermeirena. Obecnie pracują nad łóżkiem rehabilitacyjnym i aktywnym wózkiem, których konstrukcja opiera się na nowej idei.
– Na początku zawsze się wydaje, że dany produkt jest tak dobry, że nie można już nic udoskonalić, ale zawsze znajdzie się jakiś obszar, który da się jeszcze poprawić, zwłaszcza że pojawiają się nowe technologie i materiały – podkreśla Tomasz Karolczak, dyrektor działu projektowego. – Nowe produkty powstają na zapotrzebowanie rynku, a więc odpowiadają na potrzeby klientów, którzy dopytują się o coś, czego nie ma, a ponadto pojawiają się w związku z planami rozwojowymi firmy i nowych urządzeń. Są też efektem kreatywności i twórczości projektantów, którzy wymyślają nowe urządzenia i rozwiązania.
Materiał przygotowany we współpracy z firmą
Komentarze
-
Czy pracujecie Państwo nad wózkiem dla osoby niesamodzielnej z powodu niedyspozycji intelektualnej i mającej trudności w poruszaniu się na skutek zarówno tej niedyspozycji intelektualnej, jak i wtórnej, spowodowanej licznymi urazami kończyn dolnych. Innymi słowy, czy pracujecie Państwo nad wózkiem inteligentnym, przejmującym wszystkie funkcje za użytkownika, który jedynie siedzi w nim i trzyma ręce na oparciu. Plus wariant z miejscem dla drugiej osoby, wspomagającej, lecz niewydolnej krążeniowo. Jestem zainteresowana takim modelem. Pozdrawiam. Bogumiłaodpowiedz na komentarz
Polecamy
Co nowego
- Ostatni moment na wybór Sportowca Roku w #Guttmanny2024
- „Chciałbym, żeby pamięć o Piotrze Pawłowskim trwała i żeby był pamiętany jako bohater”. Prezydent wręczył nagrodę Wojciechowi Kowalczykowi
- Jak można zdobyć „Integrację”?
- Poza etykietkami... Odkrywanie wspólnej ludzkiej godności
- Toast na 30-lecie
Dodaj komentarz